Boosting the Band of Boatbuilders
A Blend of Traditional and Modern Boatbuilding
By Todd McLeish | Photographs by Jesse BurkeAs a social studies teacher at a middle school in New York City, Ariana Murphy was restless. After earning a degree in history, she had worked a half dozen different jobs—from retail employee to tour guide to theater usher—before deciding to become a teacher, and yet she still wasn’t satisfied.
So she started thinking about woodworking.
“I was designing my future home in my mind,” she says. “I did a two-week design-and-build class over the summer in Maine, I was taking woodworking classes, but it wasn’t enough. I wanted more.”
That’s when she discovered the International Yacht Restoration School’s (IYRS) School of Technology & Trades in Newport. Murphy had spent much of her life around boats, including her father’s classic wooden sailboat, and she was drawn to the idea of building one.
“I’m not a sailor, but I knew boats, and I knew Newport,” she says. “I’d heard people say that if you can build a boat, you can build anything. Everything in a boat is curves; nothing is square; everything is so complex in its joinery that it’s a great base knowledge.”
So, she enrolled in the two-year program, and she hasn’t looked back.
If you can build a boat, you can build anything.
“I’ve come to appreciate the absolute attention to detail and the painstaking hours of work that goes into the tiniest little curve, the detail that nobody might see except the boatbuilder,” Murphy says. “To make it right and make it watertight is pretty amazing. For me, it has honed my eye and my attention to detail.”
I’m not a saillor, but I knew boats.
Ariana Murphy works on her second-year project, restoring an Anderson catboat at the International Yacht Restoration School in Newport.
Rhode Island has a long and storied history of boatbuilding, from the Herreshoff Manufacturing Co. in Bristol, which built steam-powered vessels and racing yachts starting in the late 1800s, to the iconic Blount Boats Inc. in Warren and the more than 100 others of today. According to a 2018 report prepared by economists at the University of Rhode Island, the Ocean State is home to more than 200 boatbuilding and repair companies, employing nearly 2,500 people and generating almost $400 million in gross sales.
A considerable number of those working in the industry are graduates of IYRS, where students can learn not only traditional wooden boatbuilding but also marine systems (engines, electronics, hydraulics, etc.) and modern boatbuilding using high-tech materials. The school was founded in 1993 by a group of Newport residents who wanted to restore two America’s Cup J-class yachts.
“They felt that wooden yacht restoration was a dying art, and they wanted to do something about it,” says Kim Norton-O’Brien, director of development and marketing at IYRS. “For the first 15 years, boatbuilding and restoration was the only program, and students came from around the country and internationally to learn boatbuilding and ended up becoming woodworking artisans as well.”
The school enrolls about 100 students each year—a mix of recent high school graduates, career changers, military veterans, and retirees—and about 90% have a job in their field by graduation, many with multiple offers.
For Murphy, 34, the boatbuilding and restoration program is a big change of pace from her lifestyle as a harried big-city teacher.
“It’s a quieter existence,” she says. “We have a daily morning meeting to discuss what’s happening, and then it’s me hunkering down and focusing on a task for hours. The faculty do their rounds and we discuss some more, and then I’m back at it. It’s a lot of muscle memory, where you get into a kind of rhythm. It’s tunnel vision in a cool craftsman way.”
Since the program’s founding, the first year has always involved teams of three students restoring a Beetle cat, a plank-on-frame wooden sailboat that has been built the same way for a century. The boats the students work on in their second year can vary, depending on what vessels are available. Murphy and three fellow students are restoring a 14.5-foot Anderson catboat, which she describes as “beefier and more complex” than the Beetle cat and one requiring much more precise engineering.
“This whole experience has helped me hone in on what I want out of my future career,” she says. “It’s going to be a hybrid of all the things that I am. I have a faceted past, and now I’ve got to find some kind of hybrid job that takes into account my educational background and my woodworking interests.
“I came into this program with a desire to become competent in woodworking, to understand clear project management, and to be able to read plans so I could possibly get a job or apprentice as a woodshop teacher in the future,” Murphy adds. “I’m not one of those that’s going to go into a boatyard; that was never my goal. I’m not done with being a teacher.”
Most of the retiree-age students enrolled in the boatbuilding and restoration program aren’t aiming for jobs in the industry either. They are predominately hobbyists who want to learn how to build or restore a boat for their personal use and pleasure. But most of the rest end up looking for jobs at boatbuilding companies and in area boatyards. And there is plenty of demand for their skills.
Eleven graduates went to work at Mystic Seaport on the three-year restoration of the Mayflower II, including the project’s lead shipwright. Another dozen graduates—including many from IYRS marine systems and composites programs—helped to build American Magic, the New York Yacht Club’s entry in the 2021 America’s Cup yacht race. Many others end up going to work for themselves.
Social studies teacher Ariana Murphy turned to the IYRS wooden boatbuilding and restoration program to hone woodworking skills she could bring back to the classroom.
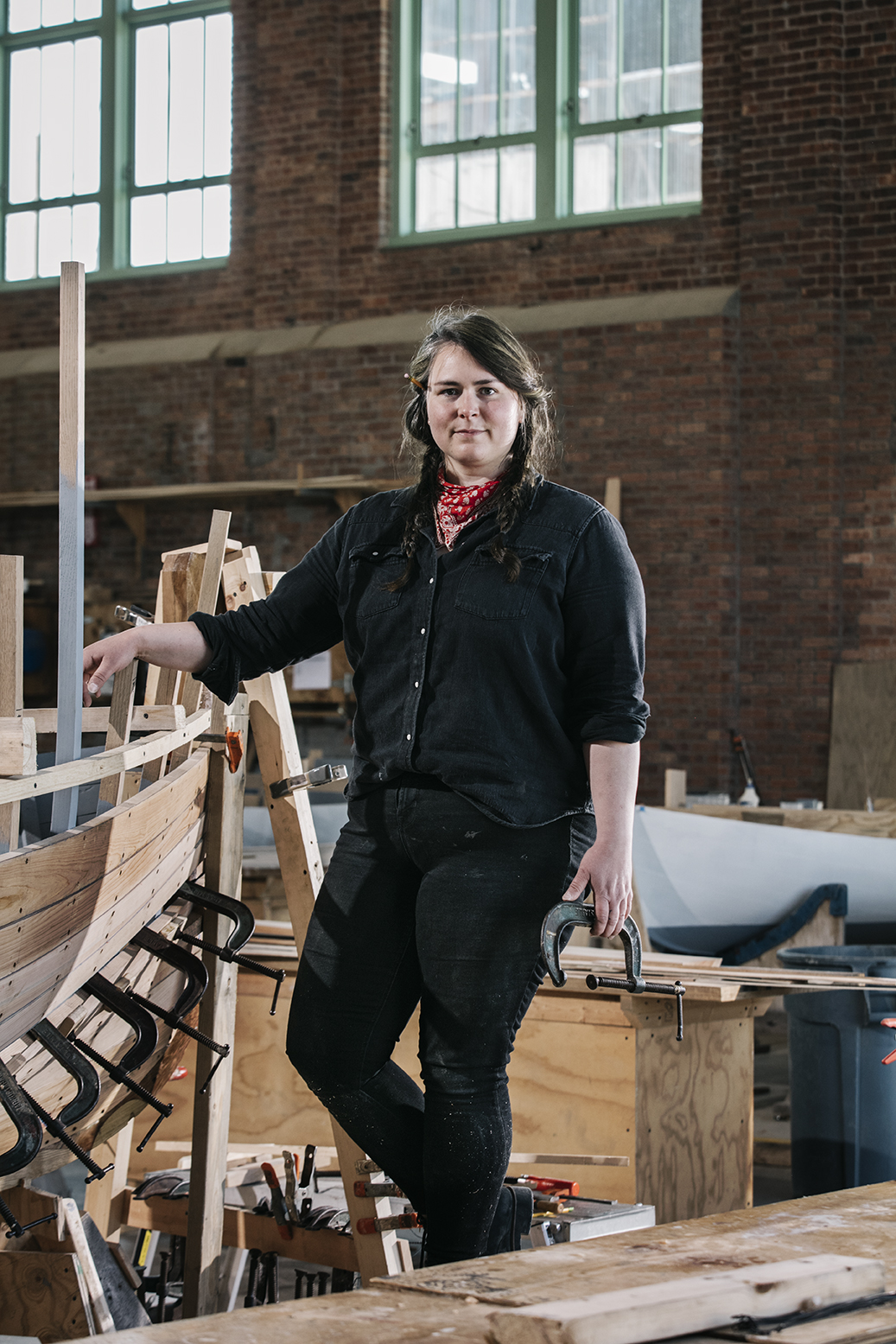
That was the path taken by Carter Richardson, an Arizona native who was introduced to IYRS while in the Navy stationed in Newport. He walked by the IYRS campus almost every day in 1997, admiring the wooden boats awaiting restoration in the courtyard, and he eventually went for a tour. After leaving the Navy and struggling to find a job after the September 11 attacks, he remembered IYRS.
“I wasn’t sure what I wanted to do, but it wasn’t what I was doing,” he says. “I figured I’d take two years at school, and if I liked it, I could move into a career in boatbuilding, and if not, then at least I’d have another skill in my quiver.”
He loved it. After graduating in 2004 and spending two years working at boatyards in Portsmouth and Mystic, Richardson and two fellow IYRS graduates started East Passage Boatwrights in Bristol. They started out exclusively focused on wooden boat restoration and maintenance, and their work soon achieved recognition, receiving top awards at the Wooden Boat Show at Mystic Seaport in 2012 and 2016 and, along with collaborators, winning the 2017 Boat Restoration of the Year from Classic Boat magazine for the restoration of a 1935 yawl once owned by Humphrey Bogart.
But while the awards were great for the business’s reputation, significant restoration projects only come along occasionally. So in 2019, Richardson commissioned a naval architect to design a 24-foot traditional open motorboat that he calls the East Passage 24.
“The idea is that this boat will become our flagship that people will come to us for,” he says. “It’s going to be our next adventure. We’ll be going into production with it soon, we’ll build each one from the keel up, and we’ll be able to customize each one to what our clients want.”
Richardson believes the East Passage 24 will help to build some consistency into his company’s work schedule and generate additional income. Although some people claim that the wooden boat industry is on the decline, Richardson’s experience proves otherwise.
“Boating skyrocketed last year because it’s seen as something you can still do safely with your family during the pandemic,” he says. “Brokers can’t keep boats in inventory. So I’m convinced there’s a market for the 24, in part because people still enjoy and are captivated by the classic look of a wooden boat. They’ve always had a huge following.”
Wooden boats aren’t for everyone, though. Many boats today are built for speed using high-tech materials. That’s why IYRS launched a composites technology program in 2010 to train students in designing and manufacturing using some of the lightest and strongest materials available. The nationally accredited program isn’t exclusively focused on designing and building boats, however.
“We think of it in terms of the materials rather than the end product,” Norton-O’Brien says. “Once you learn how to use the material and shape it the right way, you can make whatever you want. We’ve got graduates traveling the country repairing wind turbine blades, for instance.”
Composites are materials made by combining polymer resins with fiber reinforcements, like carbon fiber, glass fiber, or Kevlar. They can be molded into a wide range of objects, from low-cost bathware to high-performance spacecraft structures.
“It’s a program that appeals to a younger demographic, in part because when you build things with carbon fiber, those are things that go fast—race cars, speed boats, motorcycles,” Norton-O’Brien says. “The nature of the materials has an appeal to younger students.”
John Hatcher came to IYRS after getting laid off at a cabinetry shop in Colorado, sailing aboard windjammers in Maine, and working as a draftsman in New Jersey. Then the pandemic hit, and he decided it was time to start over again. At age 41, he’s one of the older students in the composites program and one of just three composites students focused primarily on building boats.
He got hooked on boats during a weekend trip to a lake in Colorado. “That’s when I realized I needed to get on the water more,” he says. “Sailing intrigued me because it’s not just hitting the throttle and going; there’s more to it than that. So, I went out and bought a little catamaran. Within a day I got the hull flying out of the water, I was having a great time, and then I flipped it. It was scary, but I wanted to do it again.”
He chose the six-month composites program because it could be completed relatively quickly, and the skills he would develop would complement his background in cabinetry, engineering, and drafting. When he graduates, he plans to remain at IYRS for another six months to complete the marine systems program as well.
“The wooden boatbuilding program would have been great—I’d be like a kid in a candy shop—but these two programs can be done in a year and I can be back to work again. I love wooden boats, but I’ve got a kid to feed, and it seems like there’s better pay and more job opportunities in composites.”
Those who come into the boatbuilding program are often people who haven’t succeeded in traditional higher education because they want to work with their hands.
For his final project, Hatcher is building a 7-foot fiberglass dinghy. “The goal of this project is to learn how to make a professional-grade mold that I could use to produce dinghies,” he says. “A lot of the other students’ projects are more like trying to crank out one part, but my project is learning how to do the mold. And maybe someday I can make and sell dinghies from that mold.”
His ultimate objective, though, is to work for a boatbuilding company. “I want to learn about the process of building and refurbishing boats, how boats go together, and what it’s like to work for a boat company,” Hatcher says. “Long term, I want to work on the shop floor for a couple years, then maybe move into a drafting or project management position to combine my background in drafting and cabinetry.”
Despite the higher-paying job opportunities for graduates of the composites program and the industry demand for those who can design and build with composites, the wooden boatbuilding and restoration program remains the most popular IYRS program.
“Those who come into the boatbuilding program are often people who haven’t succeeded in traditional higher education because they want to work with their hands,” says Bill Kenyon, the IYRS director of education. “When they come into Restoration Hall and stand on the balcony looking down at the work being done, it’s not uncommon for them to say, ‘I don’t know what they’re doing, and I don’t know what it’s going to lead to, but I want to do that.’”
Contact Us
Telephone: (401) 874-6805
Email: allard@uri.edu
Contributor Guidelines
Please review submission guidelines to be considered. d